In addition to special safety training for handling electricity at the time of
joining the company, we provide special training based on the Industrial
Safety and Health Act and in-house training for employees who perform
hazardous work in the field of construction work and facility management.
The Clean Crew Delight Handbook, which all cleaning personnel,
including those from partner companies, carry at all times, also contains
points to keep in mind to prevent accidents from occurring during work,
and we regularly review the handbook together.
Furthermore, the AD Solution Center collects and shares information
on incidents and accidents through the Incident and Accident System,
analyzes and identifies the causes, and raises awareness to prevent
recurrence. Information on all incidents and accidents, including occupational
accidents at contracted properties, is collected at all times and
shared with the Quality Control Division, which issues reminders to each
site as needed. In an effort to prevent recurrence, the results of these
analyses are shared and disseminated to all workplaces in the AD
Solution Center Newsletter published once a month, as well as in a
collection of accident response case studies that summarize points to
keep in mind to prevent accident recurrence during operations.
Simulation training using VR
We began incorporating virtual reality (VR) tools into our safety and health
training from September 2022, with the aim of improving hazard sensitivity
and acquiring proper work procedures through simulated accident
experiences. The VR content is designed to boost effective learning,
highlighting the following three incidents that can lead to serious
accidents in facility management operations and quizzing participants on
important points.
- Arc flash injuries caused by electrical equipment
- Falling down from a stepladder
- Falling into or over a manhole
The VR tool is permanently available at our training facility AEON delight Academy Nagahama, and a total of 1,191 people, mainly Chief Electricity Engineers, went through the VR training program in FY2023. In FY2024, we will develop new VR content related to security operations. Starting in August, we will launch an educational program that allows participants to experience initial fire response through VR as part of fire equipment maintenance training, with 29 participants attending.
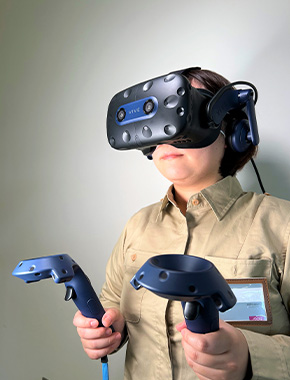
Picture of employee wearing VR goggles
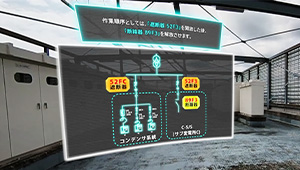
VR screen (example)
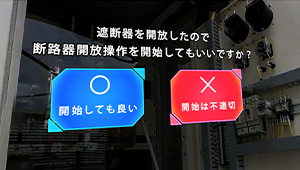
Designed to enable employees to learn important points of business procedures through a quiz